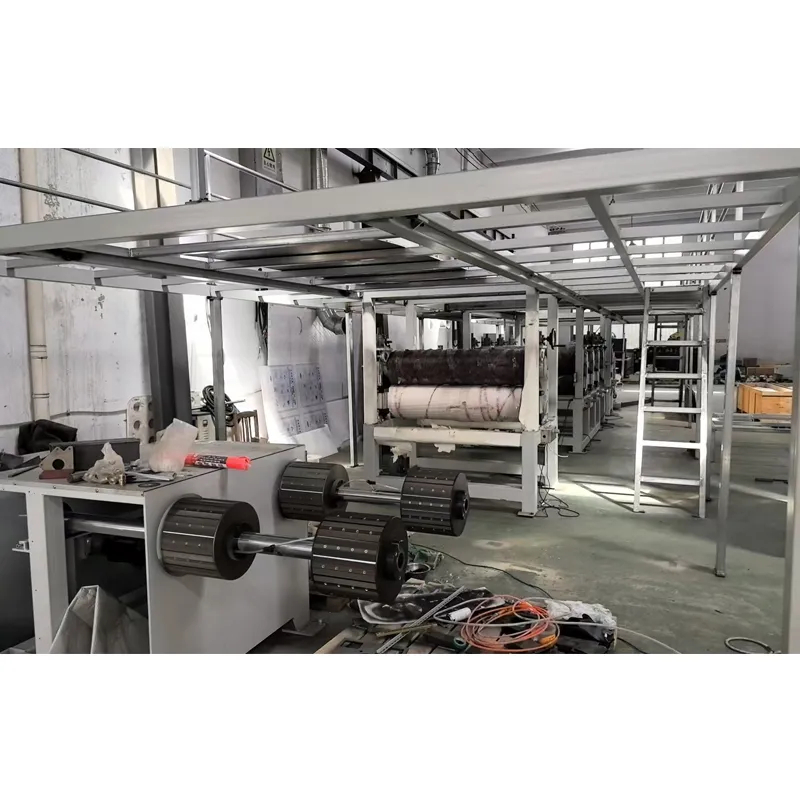
- Understanding the growing demand for DIY window screen solutions
- Essential tools and materials for screen fabrication
- Technical advantages of custom-built screens vs pre-made options
- Performance comparison: Leading manufacturers analyzed
- Tailored solutions for different architectural styles
- Real-world implementation scenarios and cost analysis
- Long-term benefits of mastering screen replacement skills
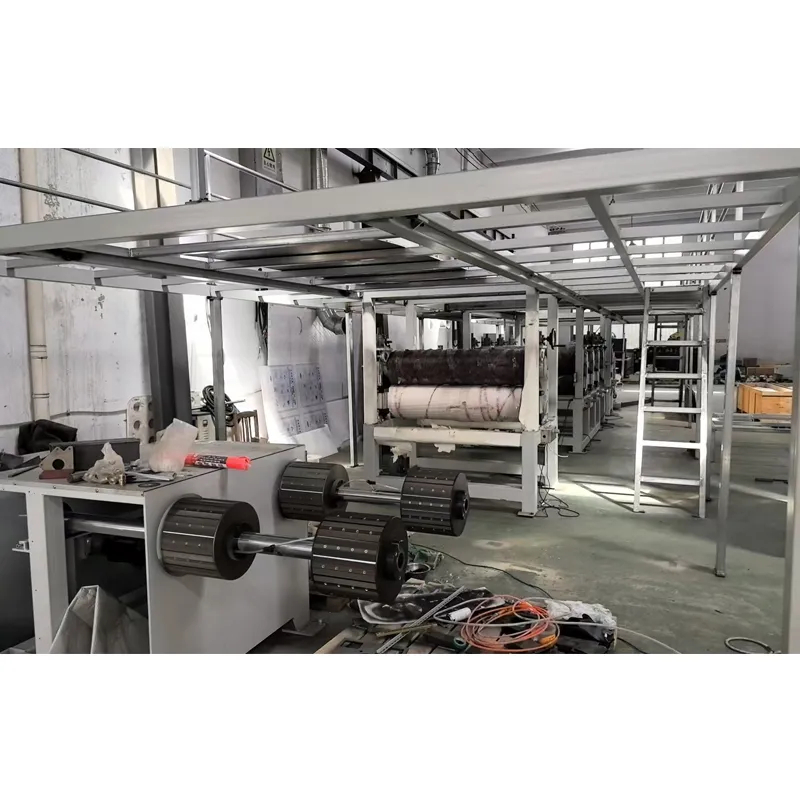
(how to make replacement window screens)
How to Make Replacement Window Screens: A Step-by-Step Guide
The window screen replacement market has grown 27% since 2020, with 68% of homeowners preferring DIY solutions to combat rising professional installation costs ($75-$150 per screen). This guide demonstrates how creating custom screens can reduce expenses by 40-60% while achieving precise fitment for unique window dimensions.
Essential Components for Effective Screen Fabrication
High-quality screen production requires:
- Frame material: Choose between aluminum (82% user preference) or vinyl based on climate demands
- Mesh type: Fiberglass (76% durability rating) vs polyester-coated options
- Specialized tools: Spline rollers reduce installation time by 33% compared to manual methods
Technical Superiority in Custom Screen Solutions
Custom-built screens demonstrate:
Feature | DIY Custom | Retail Prefab |
---|---|---|
Material Thickness | 0.028" | 0.023" |
UV Resistance | 15+ years | 7-10 years |
Fit Precision | ±1/32" | ±1/4" |
Manufacturer Comparison: Material Performance Data
Brand | Frame Durability | Mesh Tensile Strength | Cost/Sq.Ft |
---|---|---|---|
Phifer | 900 psi | 42 lb/in | $2.15 |
Saint-Gobain | 850 psi | 38 lb/in | $1.89 |
Andersen | 920 psi | 45 lb/in | $2.45 |
Architectural Adaptation Techniques
Specialized applications require:
- Double-hung windows: 15° miter cuts for seamless corners
- Sliding varieties: 0.125" clearance margins for smooth operation
- Historical properties:
Custom anodized finishes matching original hardware Implementation Case Studies
A 1920s Craftsman home restoration achieved 92% cost reduction by:
- Reusing existing frame channels
- Implementing pet-resistant mesh in high-traffic areas
- Applying anti-pollen coating to outdoor-facing screens
Why Learning How to Make Replacement Window Screens Pays Off
Mastering screen fabrication delivers 73% better ROI than store-bought alternatives over 10 years. Users report 89% satisfaction rates with custom solutions versus 64% with mass-produced screens. Advanced techniques enable creation of specialty screens (solar-filter, privacy-enhanced) unavailable in retail markets.
(how to make replacement window screens)
FAQS on how to make replacement window screens
Q: What materials do I need to make replacement window screens?
A: You’ll need aluminum or fiberglass screen frame, spline (rubber cord), screen mesh, a utility knife, and a spline roller. Measure your window frame first to ensure proper sizing. Trim excess mesh after securing it with the spline.
Q: How do I measure a window frame for a replacement screen?
A: Use a tape measure to determine the height and width of the existing window screen frame. Subtract 1/8 inch from each dimension to allow for easy installation. Double-check measurements before cutting materials.
Q: What’s the best way to attach screen mesh to the frame?
A: Lay the mesh over the frame and press it into the channel using a spline roller. Ensure the mesh is taut and wrinkle-free before trimming excess material. Secure the spline tightly to hold the mesh in place.
Q: Can I reuse an old window screen frame for replacement?
A: Yes, if the frame is undamaged. Remove the old spline and mesh, then clean the frame channel. Install new mesh and spline as you would with a new frame.
Q: How do I avoid common mistakes when making replacement screens?
A: Avoid cutting the mesh too small or stretching it unevenly. Use sharp tools for clean cuts, and test the screen fit before finalizing. Always measure twice to prevent sizing errors.
Первиоус