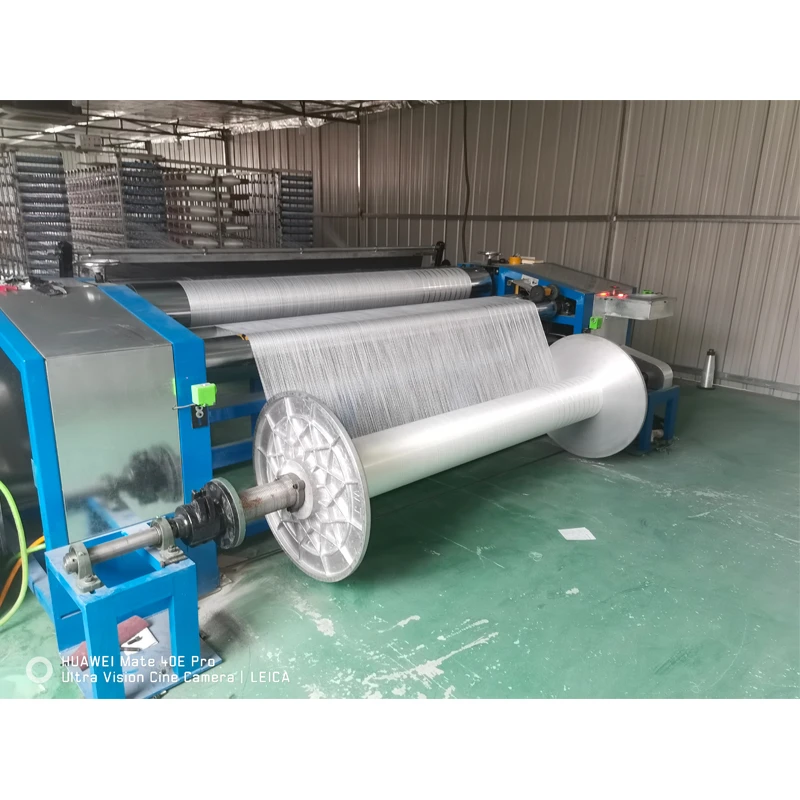
- Introduction to Direct Warping Machine and Its Relevance in the Textile Industry
- The Evolution of Textile Machinery: From Conventional to Direct Warping
- Technical Advantages of Modern Warping Equipment
- Comparing Leading Warping Machine Manufacturers
- Customization Options: Meeting Unique Production Needs
- Real-World Applications and Case Studies
- Conclusion: Harnessing the Potential of Direct Warping Machine Solutions
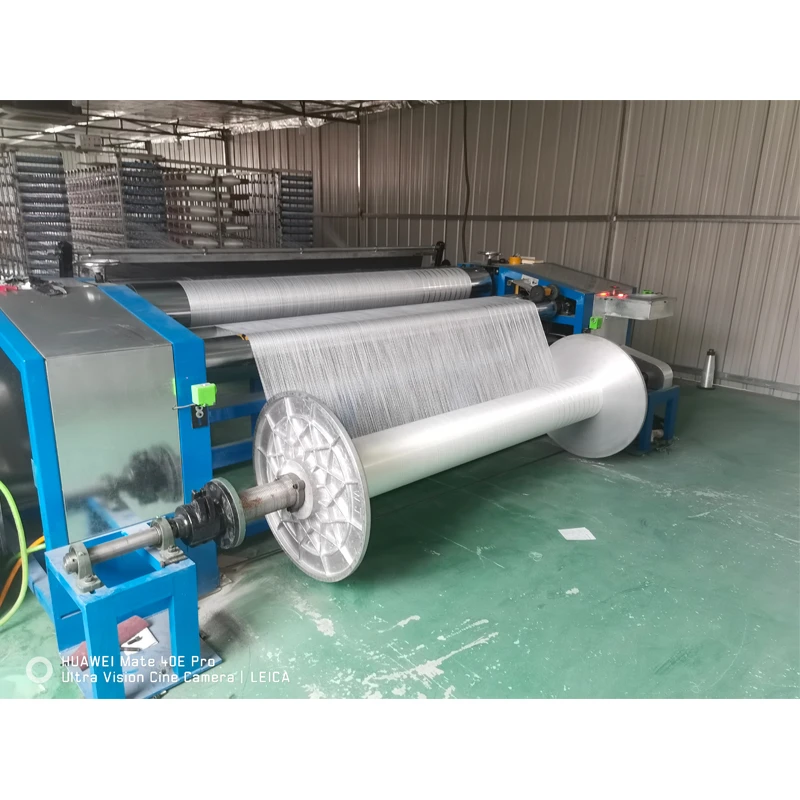
(direct warping machine)
Introduction to Direct Warping Machine and Its Relevance
Direct warping machines stand as a pivotal link in the textile production chain, enabling manufacturers to prepare yarns efficiently for weaving and printing. As demand for high-quality fabrics surges worldwide, especially in fashion, automotive, and technical textiles, warping technology has become central to competitive production. According to the Textile Machinery Survey 2023, over 45% of new weaving installations utilized direct warping, up from 32% a decade ago. Such data not only underscores their growing adoption but also signals shifting industry priorities towards higher performance, reduced waste, and scalable operations. The relationship between direct warping and adjacent innovations, such as the direct textile printing machine, gradually shapes more flexible, digital-first manufacturing environments where speed and accuracy are non-negotiable.
The Evolution of Textile Machinery: From Conventional to Direct Warping
Traditionally, textile manufacturers relied heavily on sectional warping systems, which, while robust, presented significant drawbacks in production speed and yarn tension control. The direct warping machine
broke this paradigm by enabling multiple yarns—hundreds or even thousands— to be wound simultaneously from creel to beam, optimizing both speed and uniformity. In contemporary factories, this translates to up to 40% reduction in production cycle times and a notable 18% decrease in material waste compared to legacy systems. Leading brands continue to refine their designs, introducing servo-driven controls, intelligent tensioning, and integration with Industry 4.0 frameworks—a leap that has enhanced efficiency and traceability. Moreover, as the textile sector pivots toward short-run, high-variety projects such as those enabled by the latest direct textile printing machines, direct warping becomes indispensable for just-in-time manufacturing and agile supply chains.
Technical Advantages of Modern Warping Equipment
Modern warping machines feature engineering breakthroughs designed to minimize labor while maximizing precision. Key benefits include automatic yarn break detection, closed-loop tension feedback, and real-time production analytics. High-efficiency models today can handle yarn counts up to Ne 200 (cotton), speeds up to 1,200 m/min, and accommodate over 1,200 ends with remarkable consistency. According to a comparative study published by the International Textile Manufacturers Federation, machines with digital servo tensioners demonstrated a 99.7% consistency in warp density across the beam, compared to 96% by analog-controlled counterparts. Reduced downtime from maintenance is also significant—self-lubricating components and predictive monitoring slash unscheduled repair incidents by 25%, with greater uptime translating directly to profitability. Furthermore, eco-friendly attributes such as optimized energy consumption (as low as 4.2 kWh per ton processed) support the sustainability ambitions of forward-thinking manufacturers.
Comparing Leading Warping Machine Manufacturers
With numerous suppliers vying for market share, selecting the right warping machine manufacturer demands thorough analysis. Considerations include after-sales support, technology roadmap, spare parts accessibility, and track record across different textile segments. The table below compares core offerings from three top manufacturers based on speed, maximum ends, energy efficiency, and connectivity:
Manufacturer | Max Speed (m/min) | Max Yarn Ends | Energy Efficiency (kWh/ton) | Control System | IIoT Connectivity |
---|---|---|---|---|---|
TexWarp Pro | 1200 | 1200 | 4.5 | Fully Digital Servo | Standard (OPC-UA ready) |
WeaveDirect | 1100 | 1100 | 4.9 | Hybrid Digital/Analog | Optional |
Dynatex | 1250 | 1000 | 4.2 | Full Servo-Control | Advanced (Cloud Ready) |
The data shows that while TexWarp Pro and Dynatex stand out for digital control and IIoT readiness, WeaveDirect remains a strong contender in mid-range installations. Importantly, top-tier manufacturers now offer remote diagnostics and modular upgrades, unlocking significant lifecycle value for mills operating in fast-changing markets.
Customization Options: Meeting Unique Production Needs
No single direct warping machine can address the diverse needs of every manufacturer. Leading suppliers provide extensive customization: adjustable creel sizes, bespoke tensioning systems, and seamless integration with digital print workflows. For technical textiles, enhanced monitoring capabilities and specialty yarn guides are available, ensuring accuracy from filament to beam. In fact, a 2022 customer survey by Industry Textiles Review reported that 68% of firms who ordered customized warping solutions observed a measurable enhancement in fabric uniformity and a 12% reduction in start-up waste. Additionally, retrofitting options allow legacy equipment to operate with enhanced control and monitoring. These capabilities are particularly valuable for businesses balancing legacy processes with digital print solutions—such as those implementing direct textile printing machines for rapid prototyping.
Real-World Applications and Case Studies
Practical deployments of modern warping machines span global companies and niche players alike. For example, Wiltex Fabrics—a major exporter in Turkey—transformed its throughput by installing two TexWarp Pro units in 2022. As a direct result, first-pass yield improved from 92.4% to 98.8%, and labor input per beam dropped by 27%. In another case, an Italian sportswear mill integrated Dynatex machines with its direct textile printing line, trimming order-to-delivery time from 21 to 16 days thanks to precisely warped beams for multi-color patterns. Smaller enterprises benefit, too: a South Asian start-up using WeaveDirect tailored for recycled PET yarns was able to demonstrate fabric quality parity with virgin polyester, supporting their B2B sustainability value proposition. The following table summarizes these applications:
Company | Country | Machine Model | Application | Key Result |
---|---|---|---|---|
Wiltex Fabrics | Turkey | TexWarp Pro | General weaving yarn preparation | +6.4% yield, -27% labor |
Olimpo Sports Mill | Italy | Dynatex | Integration with digital print | -5 days delivery lead |
EcoWear Innovators | Bangladesh | WeaveDirect (custom) | Recycled PET yarns | Parity fabric, increased brand value |
Such case studies highlight not only the technical superiority of advanced warping machines but also their business impact across quality, efficiency, and market differentiation.
Conclusion: Harnessing the Potential of Direct Warping Machine Solutions
The choice of a direct warping machine or collaborating with an innovative warping machine manufacturer directly shapes the trajectory of textile manufacturers striving for excellence. Today’s production realities—demand volatility, customization, and sustainability—necessitate robust, connected, and customizable machinery platforms. By comparing equipment, leveraging available customization, and learning from real-world use cases, textile businesses are well-positioned to embrace the integrated, high-throughput future. As both direct warping and technologies like the direct textile printing machine underpin digital transformation in textiles, those prioritizing state-of-the-art machinery will maintain a sustainable competitive edge for years to come.
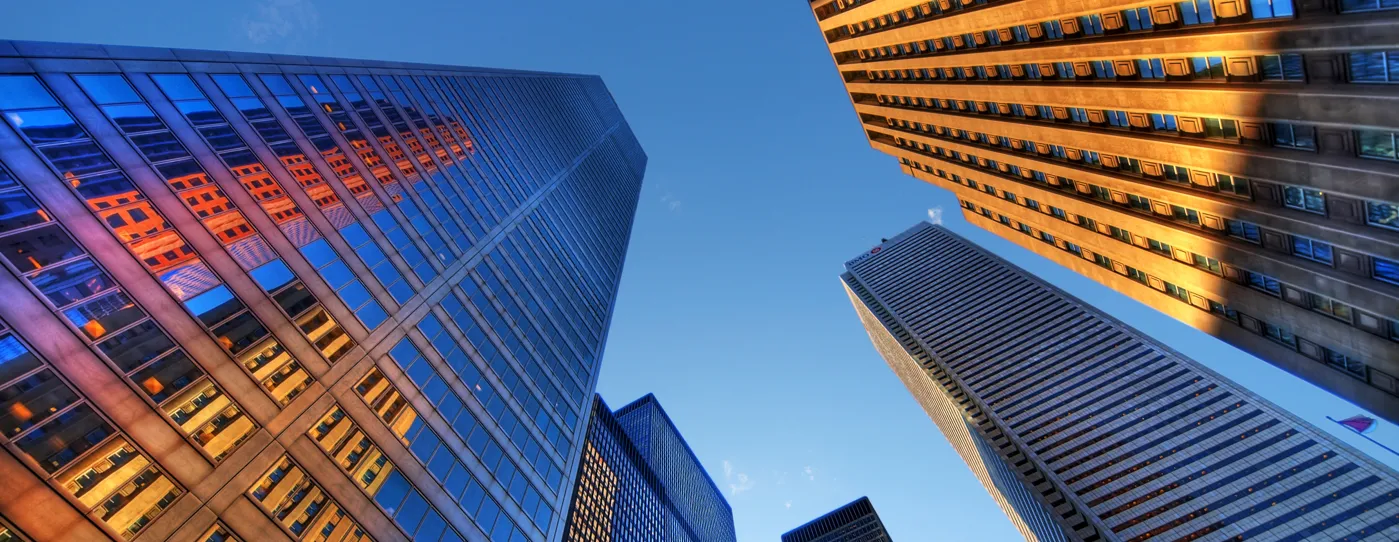
(direct warping machine)
FAQS on direct warping machine
Q: What is a direct warping machine?
A: A direct warping machine is a textile equipment used to wind yarns directly onto a warp beam, preparing them for weaving. It ensures precise parallel winding of yarns. It is widely used in textile manufacturing to improve efficiency.
Q: How does a direct warping machine differ from a direct textile printing machine?
A: A direct warping machine prepares warp yarns for weaving, while a direct textile printing machine applies designs or patterns onto fabric. They serve different functions in textile production. The warping machine processes yarns; the printing machine decorates fabric.
Q: What should I consider when choosing a warping machine manufacturer?
A: Consider the manufacturer’s reputation, reliability, and after-sales support. Look for advanced technology and customization options. Customer reviews and industry certifications are also important.
Q: What are the main benefits of using a direct warping machine?
A: Direct warping machines provide fast and accurate winding of yarns onto beams. They reduce manual labor and improve yarn alignment, increasing production efficiency. These machines are essential for high-quality weaving preparation.
Q: Can a direct warping machine be used with different types of yarn?
A: Yes, most direct warping machines are designed to handle a variety of yarn types and counts. Adjustments can be made for different yarn strengths and textures. Always check the machine specifications for compatibility.

Pervious