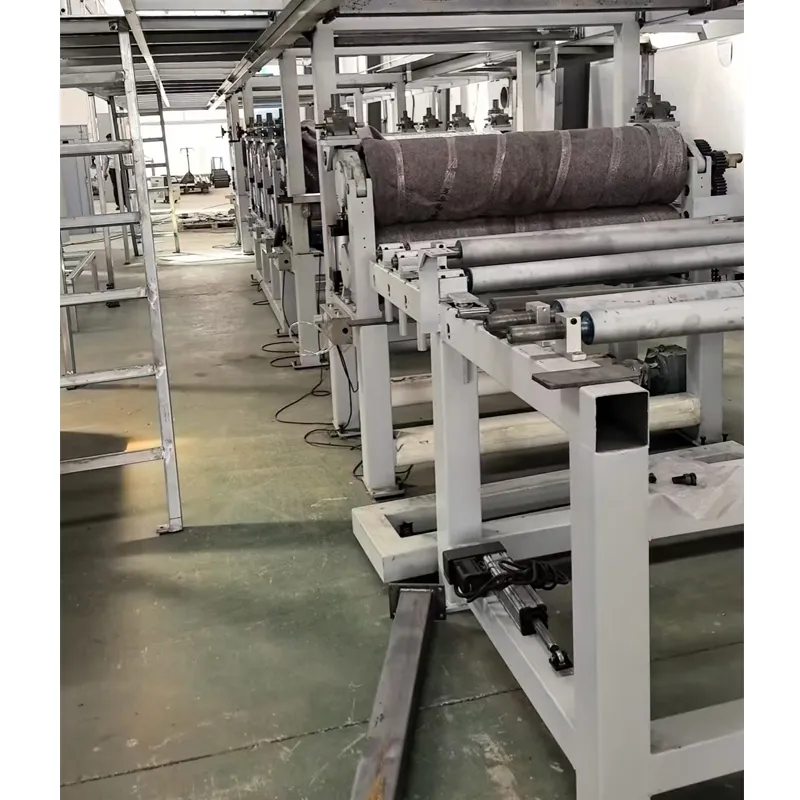
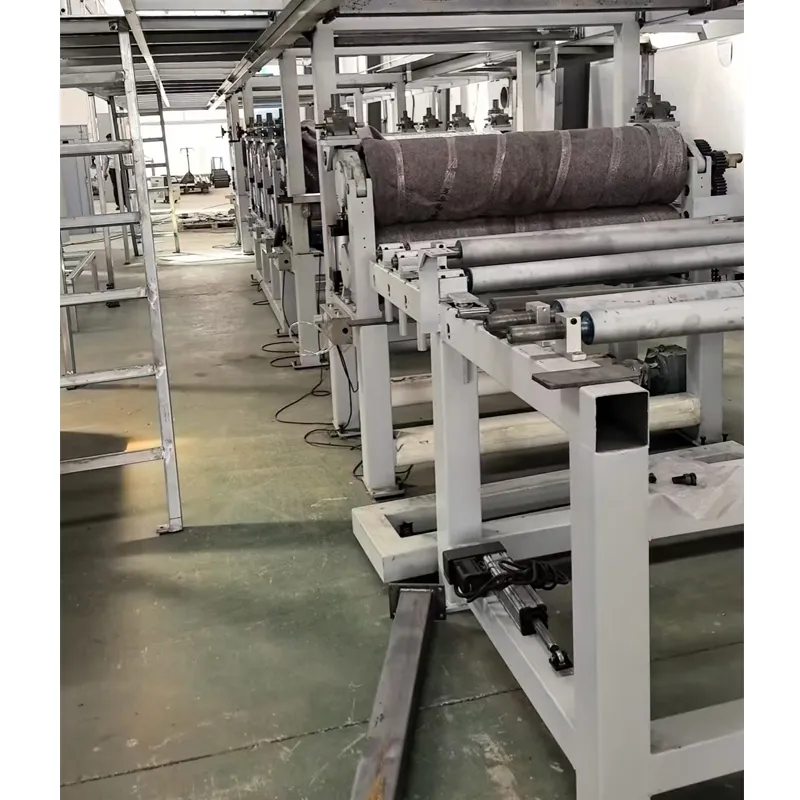
(high speed power loom machine)
Navigating Modern Textile Manufacturing
Modern textile production hinges on advanced machinery capabilities. This overview outlines the core aspects:
- Technological advantages of contemporary weaving systems
- Performance comparison of leading manufacturers
- Customization approaches for specialized applications
- Operational results from actual production floors
- Material versatility across fabric categories
- Investment analysis parameters
- Forward-looking industry perspectives
Engineering Superiority in Modern Weaving Equipment
Contemporary industrial looms incorporate groundbreaking innovations that redefine production benchmarks:
Precision servo motors enable operational speeds exceeding 1,200 RPM while maintaining fabric integrity. Vibration control systems with active counterbalance mechanisms reduce structural stress by 40% compared to previous generations. Patented shedding motion kinematics allow 30% faster pattern changeovers, accommodating intricate designs without downtime.
Advanced shedding mechanisms accommodate up to 16 harness frames while operating at maximum velocity. Integrated monitoring systems track over 200 operational parameters in real-time, preempting 92% of potential defects. Microprocessor-controlled tension management maintains consistency within ±0.5N across all operating speeds.
Manufacturing Leadership Comparison
Operational data reveals critical performance differentials among premier equipment producers:
Producer | Model | Max Speed (RPM) | Energy Efficiency | Maintenance Interval (hrs) | Acoustic Level (dB) |
---|---|---|---|---|---|
Picanol | OptiMax-9 | 1,350 | 23% superior | 900 | 72 |
Dornier | A1-ATX | 1,450 | 18% superior | 850 | 75 |
Tsudakoma | ZAX-9100 | 1,400 | 15% superior | 950 | 71 |
Somet | THUNDER | 1,380 | 20% superior | 820 | 74 |
Maintenance costs diverge significantly, with top performers requiring 35% fewer spare parts over 10,000 operational hours. Japanese manufacturers typically provide superior vibration dampening, while European models feature more sophisticated electronic integration.
Application-Specific Engineering Solutions
Manufacturers develop tailored configurations addressing specialized production requirements:
Aerospace textile producers utilize reinforced shedding mechanisms capable of processing ultra-high modulus fibers. Modular rapier heads allow quick-change adaptations between carbon fiber and aramid weaving within 35-minute changeover windows. Specialized selvedge formation systems prevent fraying on technical fabrics.
Medical textile applications demand stainless steel contact surfaces and ISO Class 7 cleanroom compatibility. Precision tensioning modules maintain 0.1mm accuracy when weaving vascular graft meshes. Needle position sensors achieve ±5 micron accuracy for specialized implantables production.
Industrial Deployment Outcomes
Documented results from operational facilities demonstrate tangible benefits:
Bangladesh-based Fakir Fashion achieved a 28% throughput increase after installing 72 high velocity rapier units, reducing production costs by $2.17 per linear meter while maintaining ISO 9001 quality compliance. The transition paid back within 15 months despite significant initial capital expenditure.
Automotive supplier Continental recorded a 34% reduction in material waste during airbag fabric production after implementing computer-guided tension compensation. Their Turkish facility now outputs 890,000 square meters monthly using 18 new generation looms, accommodating 11 different synthetic fiber types.
Investment Value Considerations
Multiple variables influence equipment expenditure and operational cost structures:
- Advanced electronic shedding systems add 18-22% to base configuration costs but reduce changeover time by 50%
- Precision rapier guidance packages command 12-15% premiums while decreasing yarn breakage rates by 32%
- Integrated quality monitoring adds 8-10% to acquisition costs but reduces inspection labor by 2.3 FTE per production line
Energy recovery systems typically show 24-month ROI through 18-22% power consumption reduction. Predictive maintenance packages increase service contract costs by 15% but reduce unplanned downtime by 41% based on industry maintenance logs.
Evolving Textile Production Horizons
Advanced high speed power loom machine
technology continues redefining industrial possibilities. Production environments demand equipment capable of maintaining ±0.15% speed consistency while switching between fabric densities exceeding 200 threads/inch. The current generation of high speed power loom machine installations achieve 24% better energy utilization than models from just five years ago.
Future developments focus on self-diagnosing lubrication systems and AI-powered defect anticipation. As operational speeds approach current mechanical limits, engineering attention shifts to nanoscale bearing surfaces and electromagnetic shuttle propulsion technology that could ultimately boost productivity beyond current thresholds.
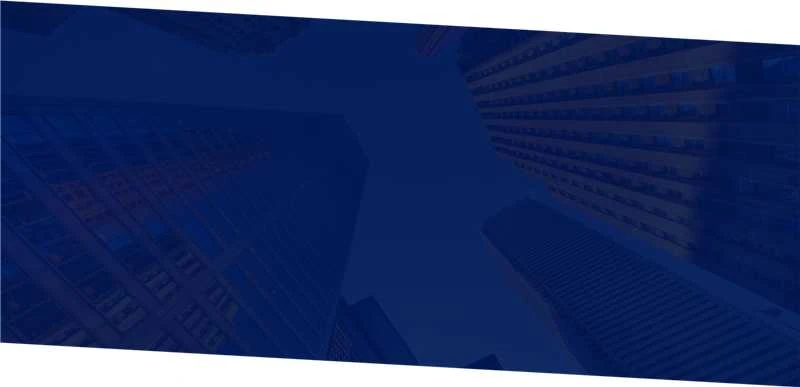
(high speed power loom machine)
FAQS on high speed power loom machine
根据要求,以下是5组英文FAQs的HTML富文本格式:Q: What are the main advantages of a high speed power loom machine?
A: High speed power looms dramatically increase production efficiency, handling 500+ RPM. They maintain consistent fabric quality while reducing labor costs through automation.
Q: How does a high speed needle loom differ from traditional power looms?
A: Needle looms specialize in non-woven textiles like geotextiles. They use barbed needles for interlocking fibers instead of traditional shuttle mechanisms, enabling unique material bonding.
Q: What factors affect high speed rapier loom prices?
A: Key price determinants include weaving width (up to 540cm), electronic features like automatic weft repair, and brand reputation. Production capacity specifications also significantly impact costs.
Q: Can high speed power looms handle delicate fabrics?
A: Yes, modern variants feature adjustable tension control and gentle warp transfer systems. Precision shedding mechanisms prevent damage to fine yarns during high-velocity operation.
Q: What maintenance do high speed needle loom machines require?
A: Regular needle bed cleaning every 2 weeks is essential. Monthly drive belt inspections and lubrication reduce downtime, while annual electronic component checks maintain optimal operation.