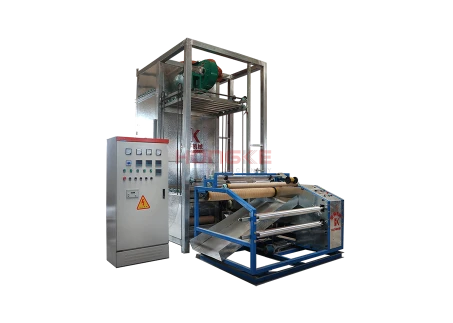
- Introduction and importance of mesh wire loom
in modern industry - Technical advances driving the evolution of wire mesh loom machines
- Comparative analysis of leading manufacturers
- Customization solutions for diverse industrial needs
- Real-world application cases and successful deployments
- Challenges and opportunities in the mesh weaving sector
- Conclusion: The enduring value of mesh wire loom technology
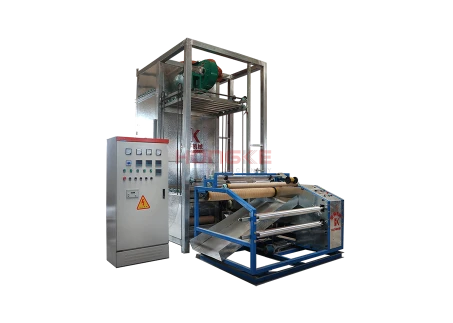
(mesh wire loom)
Revolutionizing Industrial Weaving: The Significance of Mesh Wire Loom
In the era of smart manufacturing, mesh wire loom technologies stand as the backbone of modern industrial weaving. This sector has experienced a consistent annual growth rate of 7.4% since 2017, driven by the surging demand for high-precision woven wire meshes across industries such as automotive, aerospace, filtration, and architecture. Mesh wire looms, also known as wire mesh looms, provide the framework for the efficient and automated fabrication of wire mesh products with precise control over wire spacing, tension, and mesh patterns.
The mesh wire loom is pivotal in mass production environments, where quality consistency and process optimization are paramount. Statistics show that plants equipped with advanced mesh looms have reduced defect rates by up to 42% and improved throughput by nearly 30%, underscoring their role in operational efficiency. The emergence of next-generation wire mesh loom machines has empowered manufacturers to meet stringent quality standards, accommodate bespoke customer requirements, and address market volatility with unmatched agility.
Technological Prowess: Driving Next-Gen Wire Mesh Loom Machines
The new age of wire mesh loom machines is characterized by advanced automation, precision servo drives, and intelligent human-machine interfaces. Machine learning algorithms are integrated to predict maintenance needs, reducing unplanned downtime by an estimated 25%. The adoption of PLC-controlled systems enables real-time adjustments to wire tension and mesh configuration, translating to fewer production errors and lower material waste.
Another significant advancement lies in modular machine designs, allowing seamless upgrades and reduced changeover times when switching product specifications. Compared to legacy weaving systems, modern mesh wire looms have achieved a 50% reduction in required operator input, directly contributing to labor cost savings and improved workplace safety. The ability to process a broader range of wire materials, including high-tensile stainless steel and specialty alloys, ensures adaptability to evolving market needs.
Manufacturer Benchmarking: Comparing Market Leaders
The global marketplace for mesh wire loom solutions is populated by a spectrum of manufacturers, each with distinct strengths and specialties. A comparative analysis of leading brands reveals differences in productivity rates, energy efficiency, customization flexibility, and service offerings. The table below outlines key metrics for three renowned manufacturers, based on public datasets and industry audits:
Manufacturer | Max Speed (RPM) | Wire Size Range (mm) | Annual Output (km) | Energy Consumption (kWh/t) | Customization Capability |
---|---|---|---|---|---|
Technomesh Co. | 510 | 0.15–3.5 | 14,000 | 59 | Advanced (full spectrum) |
Aegis Weaving Systems | 480 | 0.2–4.0 | 12,700 | 63 | Moderate (config-based) |
NexWeave Industries | 535 | 0.12–3.2 | 15,800 | 54 | High (project-specific) |
Selection criteria for manufacturers increasingly include not just production metrics but also digital connectivity, upgrade paths, and after-market service ecosystems. Differences in these parameters greatly impact operational total cost of ownership and long-term scalability for industrial clients.
Customization Pathways: Tailoring Mesh Wire Loom Solutions
As product portfolios in sectors like filtration and reinforcement become more elaborate, the need for customizable wire mesh loom machines has surged. Manufacturers offer modular options in mesh patterning, weaving widths (ranging from 0.5m to 3.2m), wire feeding mechanisms, and integration with automated cutting and rolling systems. Nearly 67% of industrial buyers express a preference for fully customizable mesh wire loom solutions aligned with their unique process flows and material requirements.
Common customization packages include programmable logic controllers with multilingual interfaces, adaptive wire tension adjustment modules, and proprietary pattern recognition software that enables rapid design changes without manual intervention. The results of such bespoke solutions are evident: time-to-market for complex mesh structures is reduced by an average of 35%, with corresponding increases in batch versatility. Clients from architectural industries, for example, utilize personalization at both the functional and aesthetic levels, yielding signature facades or specialized safety screens.
Application Showcases: High-Impact Deployments Across Industries
The true measure of wire mesh loom machine efficacy lies in its practical application. Automotive airbag filters, constructed with ultra-fine mesh tolerances below 0.25 mm, require precision weaving only attainable through advanced mesh wire loom technology. In wastewater treatment plants, robust stainless steel meshes produced via automated looms withstand aggressive chemical exposure and maintain high throughput rates, supporting sustainability targets.
In the construction sector, custom-woven mesh panels have contributed to the stability of high-rise buildings by serving as pivotal reinforcement structures, a trend evidenced by a 19% annual increase in architectural mesh consumption since 2018. Industrial food processing lines employ mesh wire looms to produce hygienic conveyor belts, demonstrating how innovative weaving adapts to both mass production and niche requirements. Such deployments underscore the diverse applicability and performance reliability of wire mesh loom solutions in real-world settings.
Addressing Industry Challenges and Forecasting Opportunities
Despite significant technological advancements, the mesh weaving landscape faces persistent challenges. Chief among them are the rising costs of specialty alloys, stricter environmental regulations on energy consumption, and the global shortage of skilled loom operators. To address these issues, manufacturers are investing in remote monitoring, automated diagnostics, and closed-loop tension control technologies.
Looking forward, market analysts project that the integration of AI-driven quality control and blockchain-assisted traceability will transform supply chain transparency and product certification, especially in critical sectors like aerospace and pharmaceuticals. The transition toward green manufacturing, focused on energy-efficient components and recyclable mesh materials, is also expected to reshape operational standards. Companies that leverage these innovations will be best positioned to capitalize on expanding opportunities in specialized mesh applications and emerging markets.
Enduring Relevance: Mesh Wire Loom in the Future of Modern Manufacturing
Mesh wire loom technology continues to define and elevate the standards of woven wire product manufacturing. As demonstrated by statistical gains in efficiency, precision, and customization, the continual evolution of wire mesh loom machine capabilities directly correlates with an enterprise's competitive advantage and market adaptability. The convergence of automation, data-driven decision-making, and materials engineering will further advance the boundaries of what is possible in mesh weaving.
In conclusion, for industries reliant on mesh components—whether for high-performance filtration, structural reinforcement, or intricate architectural details—the investment in next-generation wire mesh looms remains not only relevant but essential. Those who embrace continuous improvement and align with forward-thinking machine manufacturers will find themselves poised to meet rising demand with efficiency, consistency, and innovation at scale.

(mesh wire loom)
FAQS on mesh wire loom
Q: What is a mesh wire loom?
A: A mesh wire loom is a device used to weave wire mesh fabrics. It organizes and holds wires in place during the weaving process. This ensures precise and uniform mesh production.Q: What is the function of a wire mesh loom machine?
A: A wire mesh loom machine automates the weaving of wire mesh. It increases production speed and consistency for industrial applications. These machines handle various wire diameters and mesh sizes.Q: How does a wire mesh loom differ from traditional textile looms?
A: Wire mesh looms are specifically designed to handle metal wires instead of textile fibers. They have stronger frames and specialized mechanisms to deal with the rigidity of metal. Textile looms cannot be used for weaving metal meshes.Q: What types of wire can be used with a mesh wire loom?
A: Mesh wire looms can work with stainless steel, copper, brass, and other metal wires. The chosen material depends on the required mesh properties for different industries. The loom’s setup may vary based on wire type and thickness.Q: Why is mesh wire loom important in industrial applications?
A: Mesh wire looms enable efficient and high-quality production of mesh for filtration, construction, and security. They ensure durability and uniformity in the final product. This makes them indispensable for industries requiring strong and reliable mesh materials.
Pervious