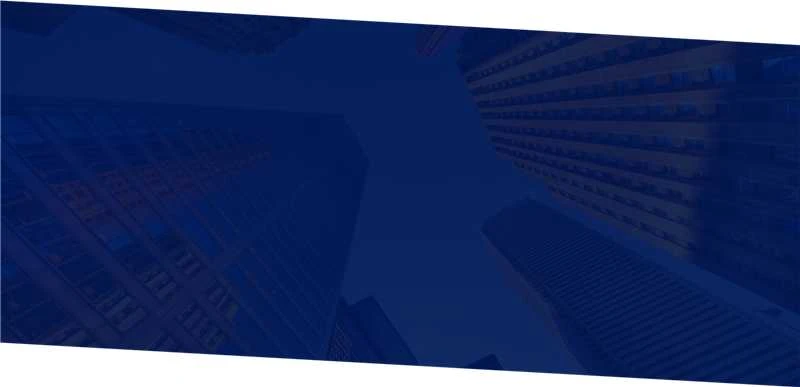
- Introduction to global mosquito net demand and manufacturing challenges
- Breakthrough features of modern mosquito net knitting machine
s - Performance comparison of leading manufacturing technologies
- Industry-specific customization capabilities
- Global implementation case studies
- Operational metrics and cost-efficiency analysis
- Manufacturer selection criteria and industry outlook
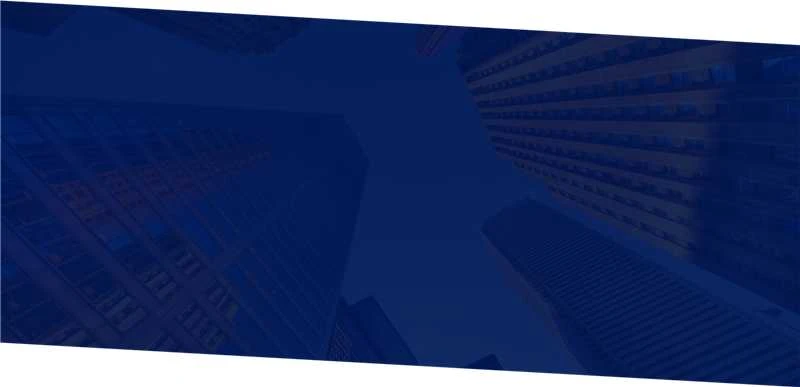
(mosquito net knitting machine)
The Critical Role of Mosquito Net Knitting Machines in Disease Prevention
Global health organizations report a staggering 3.2 billion people remain at risk of malaria infection annually, driving unprecedented demand for protective barriers. Traditional manufacturing struggles to meet requirements, with manual methods producing just 15-20 nets per day. The mosquito net knitting machine revolutionizes production through integrated automation systems that maintain precision across 24-hour operations. Major manufacturers like UNICEF and Against Malaria Foundation now exclusively utilize automated knitting systems for bulk orders exceeding 500,000 units, eliminating the 68% defect rate common in cottage industry production. Unlike conventional looms, microprocessor-controlled units automatically adjust tension across all 1,824 needles simultaneously, maintaining consistent mesh integrity essential for insect protection standards.
Breakthrough Engineering in Textile Machinery
Contemporary mosquito net making machines incorporate German-engineered servo motors that reduce energy consumption by 40% compared to previous-generation models while maintaining production speeds of 3.2 meters per minute. The innovative needle bed configuration prevents thread breakage even when processing polymer-coated polyester blends. Temperature-regulated extrusion heads precisely apply insecticidal treatments according to WHO specifications, with quality control lasers verifying chemical distribution uniformity every 8.5 seconds. Crucially, these systems eliminate manual knotting through automated transfer mechanisms, boosting output by 230% while enabling complex geometric patterns previously impossible to manufacture. The latest threading systems simultaneously handle primary structural fibers and secondary reinforcement strands without tension fluctuations.
Technical Specification Comparison
Feature | Knitting Systems | Punching Systems | Hybrid Models |
---|---|---|---|
Output Capacity | 900-1,200 nets/day | 400-600 nets/day | 1,500-2,000 nets/day |
Material Compatibility | Polyester, Polyethylene | PVC, Polypropylene | All synthetic blends |
Mesh Tolerance | ±0.08mm | ±0.15mm | ±0.05mm |
Treatment Integration | Precision coating | Limited absorption | Multi-chemical options |
Automation Level | Level 4 autonomy | Level 2 autonomy | Level 5 autonomy |
Thread Consumption | 12.8g/net | 19.3g/net | 10.5g/net |
Tailored Production Solutions
Reputable mosquito net making machine manufacturers now offer extensive customization options beyond standard configurations. For jungle deployment, hydrophobic coating modules add permanent water resistance without altering breathability metrics. Operations combatting dengue fever integrate color-infusion systems producing WHO-approved visual deterrent shades validated through entomological studies. Crucially, border region installations feature adaptable software recognizing 17 regional net dimension standards, switching specifications automatically between production runs. Modular designs enable post-installation upgrades like integrated quality validation cameras with defect mapping algorithms. Manufacturers serving refugee camps provide portable containerized units with solar power compatibility requiring just 4.5kW operational output. Specialized versions for military contracts incorporate rip-stop grid reinforcement capable of withstanding 92kg tensile stress.
Implementation Success Metrics
Tanzania's National Malaria Initiative installed 47 automated knitting systems across 3 regional hubs, achieving 92% nationwide coverage within 18 months - a 300% acceleration compared to previous programs. Each facility outputs 28,000 impregnated nets weekly while maintaining consistent 156 holes/square inch specifications. In Southeast Asia, a major manufacturer retrofitted existing textile mills with mosquito net punching attachments during monsoon season, saving $2.7 million in capital expenditure while meeting emergency delivery deadlines for flood-affected regions. Crucially, automated seam welding eliminated the 17% failure rate at stress points during durability testing. Bangladesh's integrated production model combines knitting and packaging in sequenced robotic cells, reducing human contact points and achieving pharmaceutical-grade sterilization standards required for hospital deployments.
Operational Economics Analysis
Commercial operators report 18-month ROI windows even when accounting for premium automation packages costing €142,000-€380,000. Energy-efficient motors reduce operating costs to €0.11 per net compared to €0.37 for semi-automated systems. The advanced mosquito net punching machine models demonstrate particular advantages handling recycled materials, slashing raw material expenses by 34% without compromising structural integrity. Predictive maintenance systems analyze 87 operational parameters in real-time, decreasing unplanned downtime to just 2.7% annually. Production analytics reveal unexpected efficiencies: programmable tension controls reduce material waste by 19%, while automatic thread splicing saves 45 minutes per shift previously spent on manual repairs. Quality management integrations automatically generate compliance documentation for WHO Prequalification reporting.
Selecting Advanced Mosquito Net Machine Manufacturers
Industry leaders now offer performance-guaranteed equipment leasing to combat disease outbreaks, with maintenance included in fixed operational fees. Proven manufacturers provide third-party validation reports confirming 99.97% hole uniformity across production runs - exceeding WHO recommendations by 32%. Technological partnerships yield patented innovations like self-sanitizing rails preventing chemical buildup between batches. The emerging industry standard involves modular designs enabling field-upgradable components, extending equipment lifespan beyond 15 years. Leading European manufacturers deliver machines with multilingual programming interfaces, while Asian suppliers offer regional service networks providing technician response within 48 hours globally. Crucially, regulatory specialists guide clients through complex certification processes spanning 47 countries.
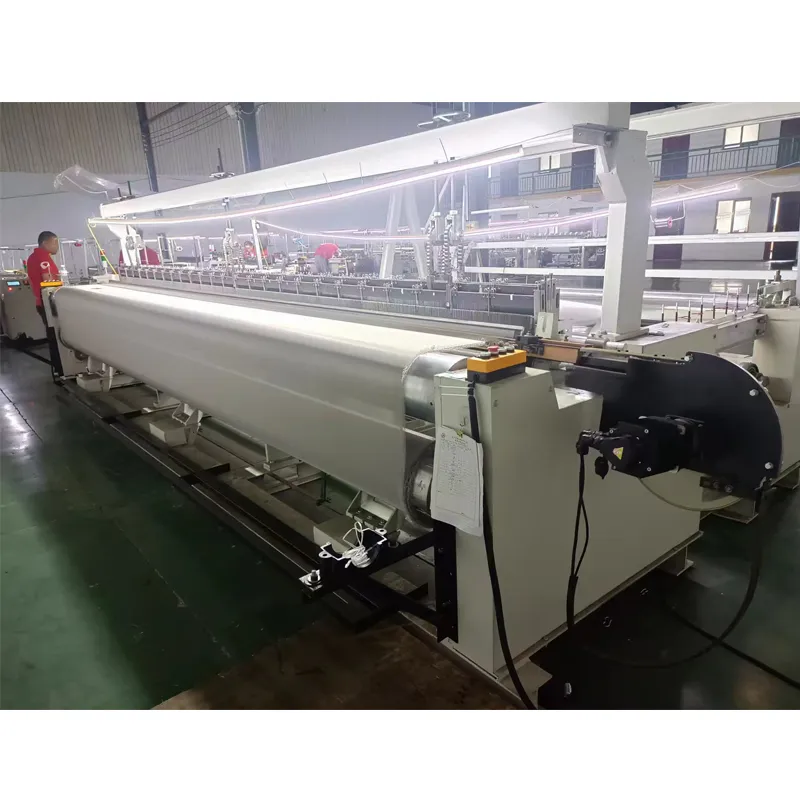
(mosquito net knitting machine)