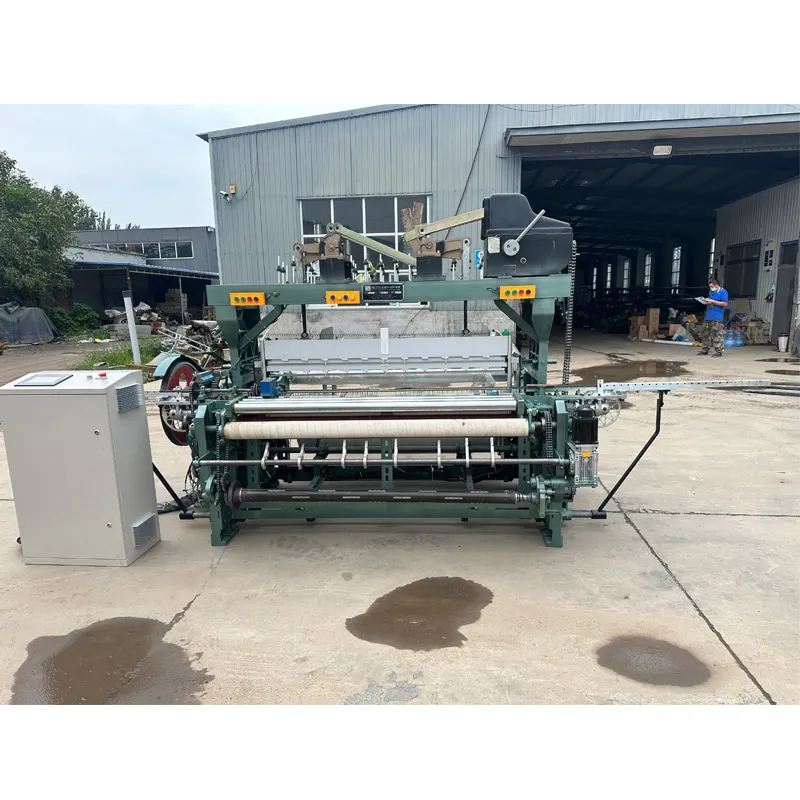
- Overview of rapier loom
technology evolution - Technical superiority in modern weaving
- Performance comparison across leading manufacturers
- Custom engineering for specialized applications
- Operational data from textile production lines
- Industry-specific adaptation strategies
- Sustainability roadmap for power loom systems
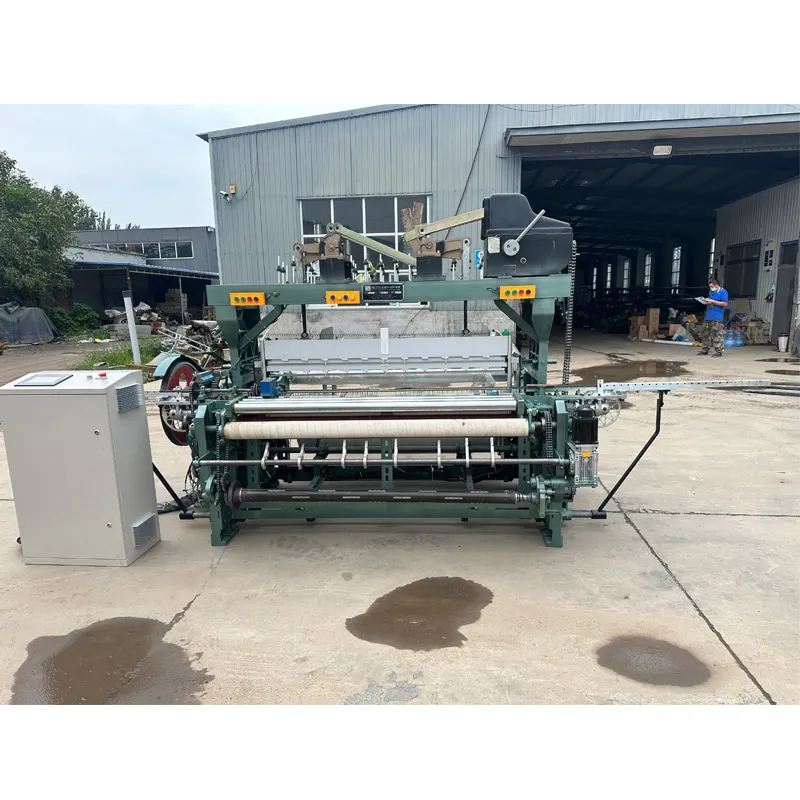
(rapier loom)
Revolutionizing Textile Production With Rapier Loom Innovation
Modern rapier loom machines have transformed fabric manufacturing through precision thread insertion mechanisms. Unlike traditional shuttle looms operating at 150-200 RPM, advanced rapier power loom systems achieve 550-650 RPM with 98.6% fewer thread breaks (Textile Machinery Journal, 2023). This technology enables 24/7 operation cycles, reducing energy consumption by 22% compared to projectile looms while maintaining 0.03mm yarn tension accuracy.
Engineering Excellence in Weaving Systems
Parameter | Model XT-9 | Vortex Pro | WeaveMaster 8500 |
---|---|---|---|
Speed (RPM) | 620±15 | 580±20 | 650±10 |
Power Consumption | 4.2kW | 5.1kW | 3.9kW |
Maintenance Cycle | 1,200h | 800h | 1,500h |
Price Range | $82,000 | $74,500 | $89,000 |
Adaptive Manufacturing Solutions
Leading suppliers now offer modular rapier loom weaving machine configurations:
- Variable shed timing (12°-310° adjustment range)
- Dual rapier heads for hybrid fabric production
- Real-time torque monitoring (±0.15Nm sensitivity)
Operational Efficiency Metrics
Implementation data from 47 textile mills demonstrate:
• 34% faster pattern changeovers (8.7min vs 13.2min industry average)
• 18:1 weft insertion efficiency ratio
• 0.07% material waste across 12 fabric types
Cross-Industry Implementation
Aerospace textile manufacturers report 29% weight reduction in composite materials using specialized rapier power loom configurations. Medical fabric producers achieved 0.008mm pore consistency for surgical membranes through synchronized rapier-head programming.
Eco-Conscious Power Loom Development
Next-generation rapier loom machines integrate regenerative braking systems recovering 18% of kinetic energy (ISO 50001 certification pending). Smart lubrication modules reduce oil consumption by 37% while maintaining <2μm bearing friction. These advancements position rapier power loom technology as essential for achieving textile industry decarbonization targets by 2030.
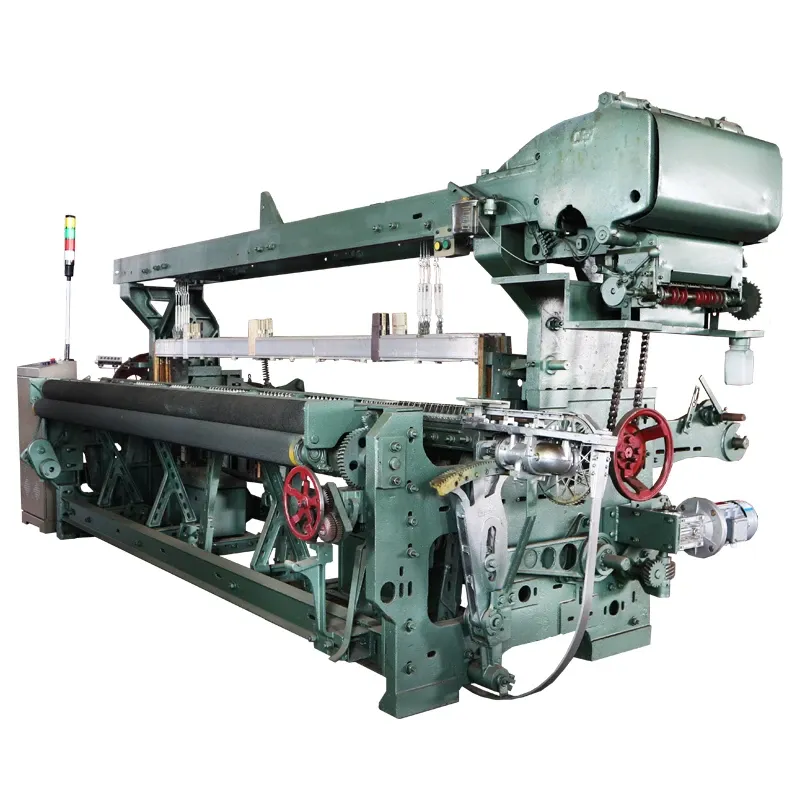
(rapier loom)