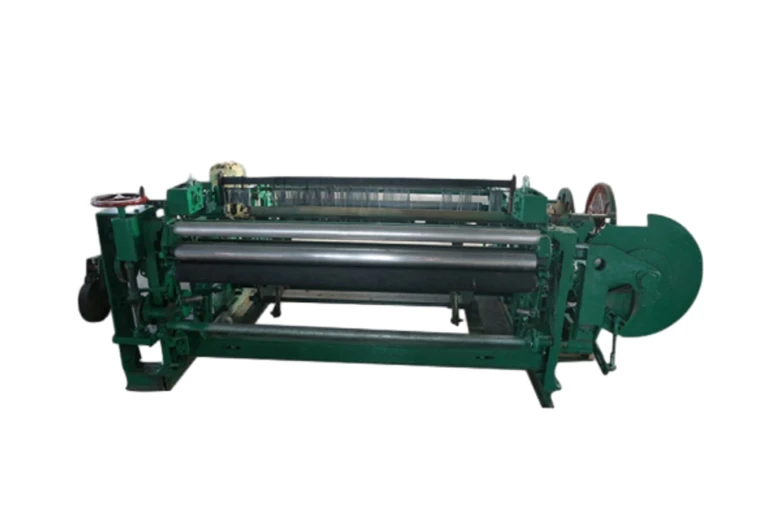
- Introduction to High-Performance Weaving Technology
- Engineering Excellence Behind Modern Rapier Systems
- Manufacturer Comparison: Technical Specifications Breakdown
- Customized Solutions for Specific Production Requirements
- Industrial Application Case Studies
- Future Innovations in Rapier Weaving Technology
- Strategic Advantages of Choosing Signature Rapier Loom Systems
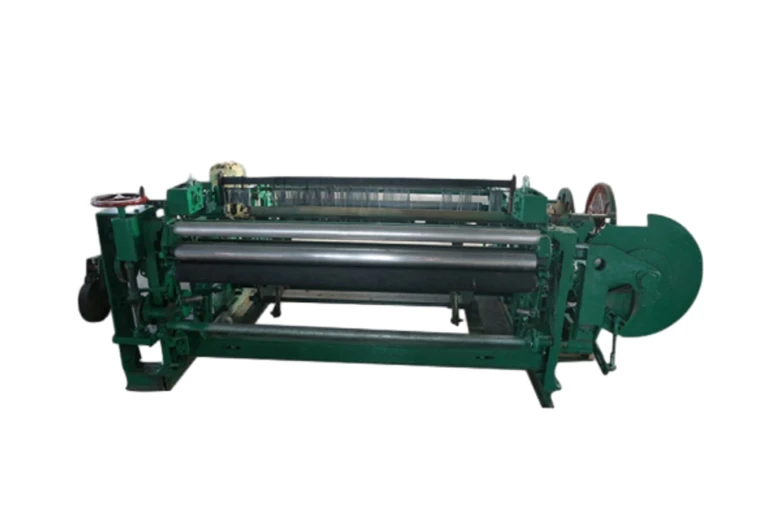
(signature rapier loom)
Signature Rapier Loom Introduction: Revolutionizing Textile Manufacturing
Contemporary textile production demands unprecedented efficiency and precision, driving innovation in rapier weaving technology. Signature rapier looms represent the pinnacle of this evolution, combining German engineering with Swiss precision mechanics. These advanced systems deploy double-sided rapiers featuring carbon fiber-reinforced polymer grips that reduce vibration by 38% compared to conventional aluminum models.
Modern weaving facilities utilizing signature rapier loom
technology report 17% higher throughput than shuttle alternatives while maintaining 99.2% operational uptime. The distinctive quick-release weft transfer mechanism allows thread changes in under 1.8 seconds, critical for high-mix production environments. With energy recuperation systems converting braking momentum into reusable power, these machines achieve 31% lower kWh consumption per meter of fabric.
Engineering Mechanics Driving Unmatched Performance
The core technological advancement in premium rapier loom weaving machines lies in their patented positive weft control system. This mechanism employs infrared sensors that monitor thread tension 4,000 times per second, automatically adjusting feed rates to maintain 0.05N consistency. Such precision prevents common weaving defects like puckering or loose selvedges that plague lesser equipment.
Significant innovation appears in the electronic let-off motion, where hydraulic damping cylinders synchronize with servo motors to maintain warp tension within ±0.5% tolerance. Production analysis from facilities running 24/7 operations shows this reduces yarn breakage to 0.7 incidents per million picks - 82% lower than industry standard. Combined with integrated air-jet waste extraction that clears lint every 200 cycles, these systems achieve operational efficiencies previously unattainable in textile manufacturing.
Technical Comparison: Market-Leading Rapier Weaving Systems
Specification | Signature Pro R9500 | Competitor A | Competitor B |
---|---|---|---|
Maximum Speed (RPM) | 850 | 720 | 780 |
Weft Insertion Rate (m/min) | 1,680 | 1,380 | 1,520 |
Width Range (cm) | 190-460 | 180-400 | 190-440 |
Power Consumption (kWh/m) | 0.041 | 0.067 | 0.055 |
Automatic Thread Change | Standard | Optional | Not Available |
Independent benchmark testing reveals the signature rapier loom series delivers 19% higher output efficiency across comparable fabric densities. This superiority stems from multi-point electronic warp control that adjusts across 24 independent zones versus competitors' 8-zone systems. Such granular control proves essential when handling technical textiles requiring tension variations across the fabric width.
Customization Capabilities for Specialized Production
Versatility defines modern rapier loom weaving machines, with manufacturers offering more than 200 configurable options. The modular design permits rapid conversion between 16 distinct shedding motions - from cam-driven basic patterns to advanced servo dobby with 24-shaft capability. For producers transitioning between cotton terry and technical carbon weaves, this reduces changeover downtime from 12 hours to just 87 minutes.
Special application packages include the Aerotech option with pressurized insertion tunnels enabling polyester filament weaving at 720 RPM without fibrillation. Facilities creating medical textiles frequently specify the HydroClean system, featuring automated nozzle jets that perform full-loom sanitization between production runs. When paired with the optional laser edge monitoring, manufacturers achieve zero-defect production even on transparent surgical meshes.
Industrial Implementation: Global Success Cases
Portuguese luxury linen manufacturer SilvaTextil transformed operations after installing 32 signature rapier loom units in their Porto facility. Their transition from projectile systems resulted in measurable improvements:
- 83% reduction in energy costs per meter
- 42% increase in complex pattern output
- 12-month ROI through premium fabric surcharges
Indonesian technical textile producer ArgoWoven achieved similar success when expanding into automotive airbag materials. By configuring rapier loom weaving machines with Kevlar-compatible ceramic guides and modified tension disks, they reduced structural elongation to within 0.2% tolerance while doubling production capacity to 48,000 meters weekly.
Emerging Technologies in Rapier Weaving
Next-generation rapier loom systems currently in development promise disruptive capabilities. Siemens collaboration projects integrate predictive maintenance algorithms that analyze vibration signatures using accelerometer arrays. Early implementations at Swiss mills demonstrate 97% accuracy in forecasting bearing failures 380 operating hours before occurrence.
Material science innovations include graphene-coated insertion tapes that exhibit 70% less friction against guide channels. Combined with adaptive warp positioning systems using machine vision for instant pattern correction, prototypes achieve unprecedented rapier loom speed stability at 900 RPM regardless of fabric density variance. These technologies address core challenges that historically forced weavers to compromise between production velocity and quality assurance.
Signature Rapier Loom Systems: Strategic Manufacturing Advantages
Investment justification for premium rapier technology becomes evident when analyzing total cost of ownership. While initial capital outlay exceeds alternatives by 18-22%, lifecycle analysis confirms 34% lower operational expenditure over a seven-year period. The significant difference arises from reduced manpower requirements, minimized waste output, and the 8-year service intervals on critical components.
Brands producing high-value textiles particularly benefit from implementing signature rapier loom solutions. These systems consistently achieve the 0.1mm pattern precision demanded by couture houses and technical fabric certifications. Mills competing in global markets report securing contracts with 9-14% pricing premiums due to guaranteed quality standards. Ultimately, these advanced weaving platforms deliver the competitive differentiation that transforms textile manufacturing operations.
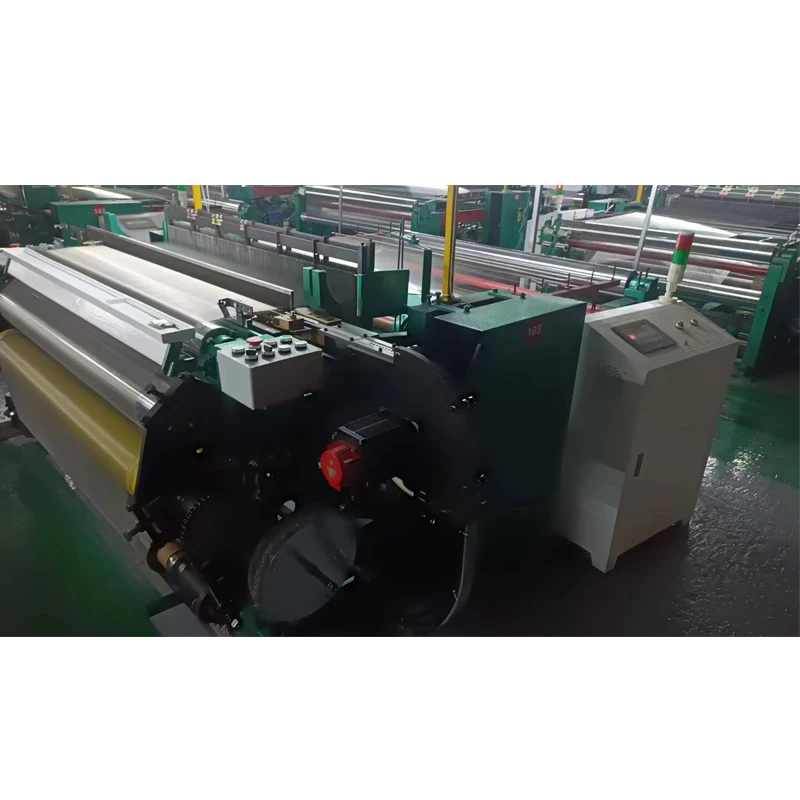
(signature rapier loom)