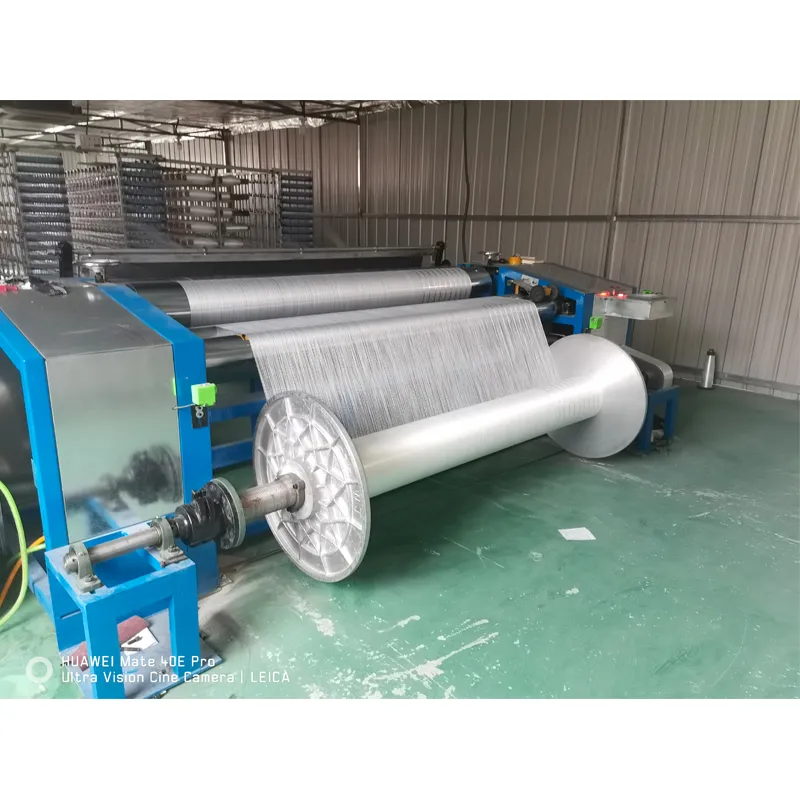
- Introduction to textile weaving machine
s and their industrial significance - Technological advancements in textile weaving equipment
- Comparative analysis of weaving, printing, and compacting machines
- Key manufacturers and their product metrics
- Customized integration and optimization solutions
- Industrial success stories and application case studies
- Conclusion summarizing textile weaving machine innovations
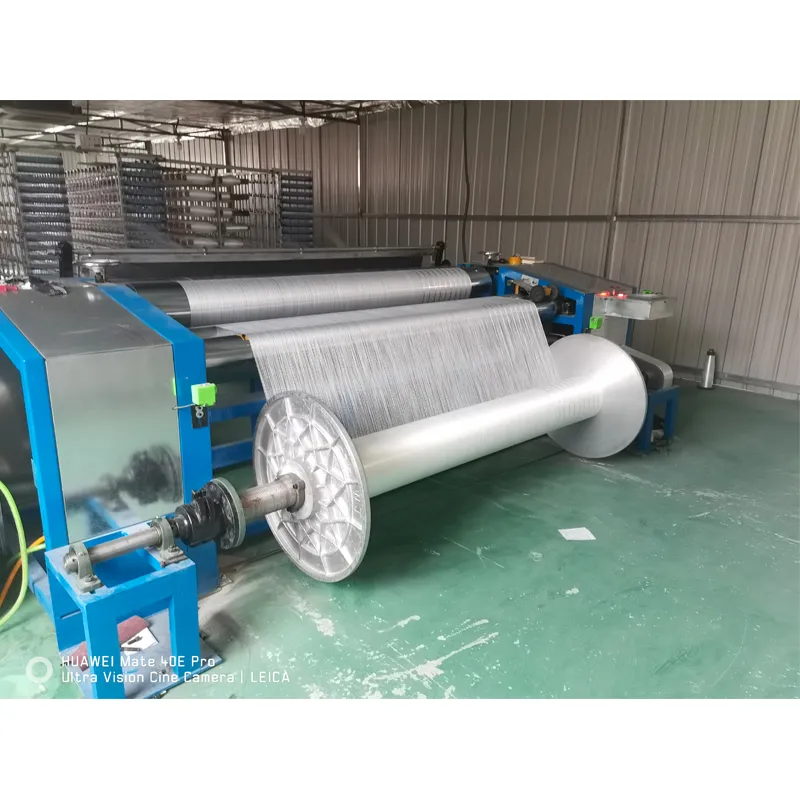
(textile weaving machine)
Textile weaving machine: Backbone of Modern Fabric Manufacturing
The global textiles industry has experienced exponential growth, fueled by technological innovation and rising consumer demand. Textile weaving machines form the heart of this sector, driving fabric production with unmatched speed and efficiency. According to recent industry data, the global market for textile weaving machines is projected to surpass USD 7.1 billion by 2026, growing at a CAGR of 5.8% from 2021. These machines have transformed from manually operated looms to advanced, digitally-controlled solutions over the last decade, significantly raising productivity and fabric quality.
Today’s weaving technologies offer unprecedented levels of precision and automation. Coupled with related machinery such as textile printing machines and compacting machines in textile processing chains, these sophisticated systems enable the creation of highly differentiated products. Key performance metrics such as fabric throughput, defect rates, energy efficiency, and operational costs are now closely monitored, with industry leaders investing heavily in R&D to push these benchmarks. The continuous evolution of textile weaving machine capabilities is at the core of sustainable competitiveness for fabric manufacturers worldwide.
Technological Advances Redefining Weaving and Fabric Finish
Technological innovations in textile machinery have revolutionized not only weaving but the entire chain of textile production. Three critical areas exemplify this evolution: digitization, automation, and smart sensors. Integration of IoT devices now allows real-time monitoring of loom performance, minimization of downtime, and rapid defect identification, with some systems reporting up to 30% reduction in waste compared to legacy equipment.
The synergy between textile weaving machines, textile printing machines, and compacting machines in textile finishing has become a defining feature of advanced production lines. The latest machines feature touch-screen interfaces, predictive maintenance platforms, and AI-based fabric inspection systems capable of detecting microflaws unattainable by human inspectors. In printing, digital solutions have enabled full-color, rapid custom design applications with throughput ranges exceeding 1,200 square meters per hour. Meanwhile, compacting machines guarantee dimensional stability and improved textile feel, closing the loop on fabric quality.
Dynamic Comparison: Weaving Machines, Printing Machines, and Compacting Solutions
Understanding the distinct capabilities of textile weaving machines, textile printing machines, and compacting machines in textile operations is essential for strategic investments. The table below presents vital performance metrics for leading industrial models currently available:
Machine Type | Model | Fabric Throughput (meters/hour) |
Energy Consumption (kWh/1000m) |
Automation Level | Defect Rate (%) | Customization Options |
---|---|---|---|---|---|---|
Textile Weaving Machine | LoomMaster 5000 | 950 | 22.5 | Full (AI core) | 0.13 | Extensive (yarn type, width) |
Textile Printing Machine | PrintJet Pro DTX | 1200 | 35.5 | Full (Digital control) | 0.07 | Custom patterns, colors |
Compacting Machine in Textile | CompaForce 600 | 800 | 19.8 | Semi-Automatic | 0.02 | Pressure, temp. settings |
The data underscores varying strengths—textile weaving machines excel in mechanical versatility, printing machines deliver unrivaled design freedom, while compacting machines assure product quality. Optimal results are achieved when these systems are selected and configured in alignment with end-product objectives.
Vendor Performance and Specialist Evaluations
Across the spectrum, several manufacturers distinguish themselves by advanced engineering, extensive after-sales support, and adaptability to diverse industrial demands. Pioneer organizations such as Itema Group, Picanol, and Toyota Industries consistently lead in textile weaving machine innovation. On the printing front, Kornit Digital and Epson set benchmarks for resolution and print consistency, while Bruckner and Mahlo excel in compacting solutions for textiles.
Assessment criteria among users typically include throughput levels, cost per meter, operational durability, and software integration. Surveys indicate that companies leveraging high-end weaving machines report 98.6% uptime and 12% reduction in maintenance costs after modernization. Print machines with intelligent ink delivery record a 28% cut in ink usage compared to standard models. With growing demand for sustainable manufacturing and real-time data, providers focus increasingly on modular upgrades and eco-efficiency.
Tailored Integration: Designing Solutions for Unique Production Needs
No two textile manufacturing operations are identical—customization and flexibility have become hallmarks of competitive success. Modern textile weaving machines are highly adaptable to specify yarn types, weaving patterns, and production speeds. Similarly, digital textile printing machines now offer on-demand batch changes, crucial for fashion and technical textiles requiring personalization within lean production cycles.
Integration between weaving, printing, and compacting machines is supported by unified control platforms, enabling seamless transition across stages and reducing manual intervention. Consulting services for layout simulation, workflow optimization, and digital twin modeling help manufacturers visualize and upgrade plant efficiency before implementation. For instance, a mid-sized manufacturer seeking accelerative lead times and multi-fabric agility can specify weaving looms with quick-change beam systems, pair them with high-velocity printers, and finish with programmable compactors tuned to target fabric softeners, all within a smartly orchestrated digital environment.
Industrial Impact: Noteworthy Application Cases
The impact of advanced textile weaving machines, alongside printing and compacting equipment, can be witnessed across multiple industries—from apparel and upholstery to technical textiles and automotive. A large-scale textiles group in Turkey, for instance, recently adopted a digitally networked line featuring dual LoomMaster 5000 looms, PrintJet Pro DTX printers, and CompaForce 600 compactors. Results included a 27% spike in fabric output within the first quarter, defect rates below 0.1%, and lead time reduction from supplier to client by 18 days.
In the Asia-Pacific region, a major uniform manufacturer integrated an AI-driven weaving-printing-compacting chain. Subsequent process traceability and automatic quality reports met international ISO standards, opening new export markets. Similarly, a European home textile label leveraged the customization potential of these systems to deliver seasonal batches in weeks rather than months, achieving 40% faster design-to-delivery cycles. Such cases affirm the transformative benefits of investing in the right combination of textile machinery and line configuration.
Evolution and Future Prospects for the Textile Weaving Machine Landscape
Textile weaving machines now set the standard in precision-driven fabric production, integrating seamlessly with textile printing machines and compacting machinery for end-to-end efficiency. As market pressures heighten and consumer trends evolve, successful manufacturers will increasingly depend on modular, data-rich systems that enable agility without sacrificing quality. The pace of innovation continues to accelerate with the adoption of AI, IoT, and sustainable engineering principles.
Looking forward, investment in next-generation textile machinery is not simply an operational upgrade, but a strategic imperative. Manufacturers embracing digital transformation and customization will be best positioned to deliver on-demand fabric solutions aligned with global standards. The textile weaving machine stands as both a foundational tool and a symbol of industry progress—its evolution synonymous with the fabric of tomorrow.
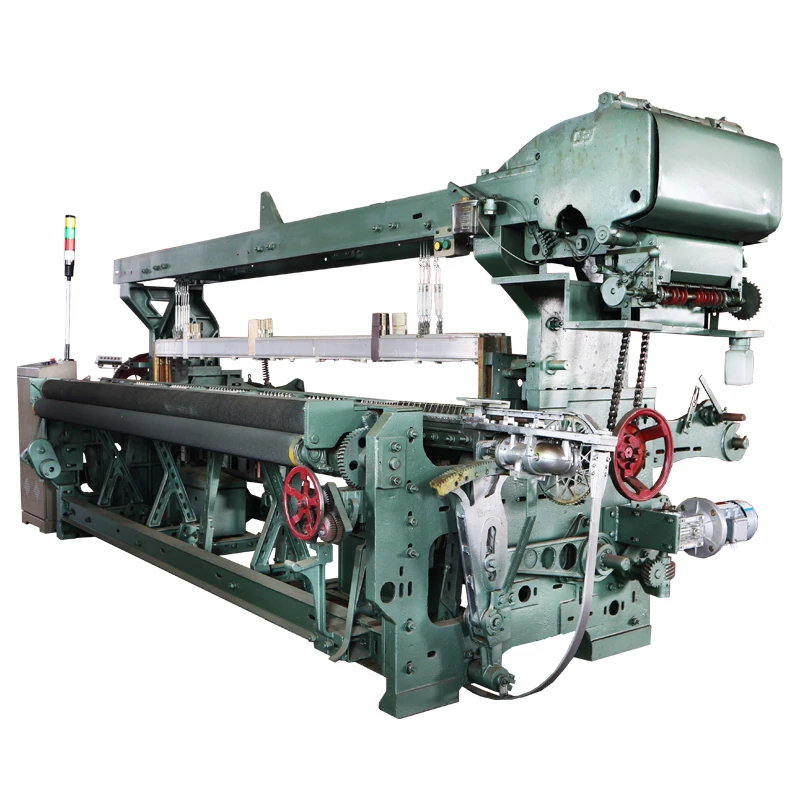
(textile weaving machine)
FAQS on textile weaving machine
Q: What is a textile weaving machine?
A: A textile weaving machine is equipment used to interlace warp and weft threads to produce fabric. It operates either manually or automatically in textile manufacturing. Weaving machines are essential in large-scale cloth production.Q: How does a textile printing machine differ from a weaving machine?
A: While a weaving machine creates fabric, a textile printing machine adds patterns or designs to finished textiles. Printing machines use techniques like screen, digital, or rotary printing. Essentially, weaving forms the fabric; printing decorates it.Q: What is the function of a compacting machine in textile processes?
A: A compacting machine in textiles pre-shrinks and stabilizes knitted fabrics to prevent further shrinkage. It smoothens and compacts the fibers after finishing processes. This ensures the fabric maintains consistent dimensions and softness.Q: What factors should I consider when choosing a textile weaving machine?
A: Consider the type of fabric, production speed, automation level, and maintenance requirements. It's also important to check the compatibility with other textile equipment. Budget and after-sales service are crucial factors as well.Q: Can I integrate a textile weaving machine with other machines like compacting and printing machines?
A: Yes, textile weaving machines are often integrated with compacting and printing machines for streamlined production. This integration increases efficiency and allows continuous fabric processing. Ensuring machine compatibility is important for optimal workflow.
Pervious