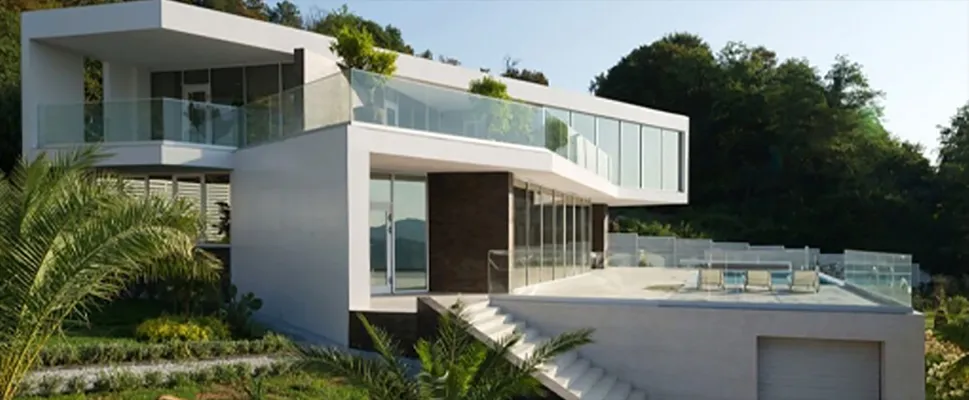
- Industry Overview & Market Impact
- Technological Advancements in Modern Machinery
- Performance Comparison: Leading Manufacturers
- Customized Solutions for Diverse Textile Needs
- Energy Efficiency & Sustainability Metrics
- Real-World Application Case Studies
- Future-Proofing Production with Smart Textile Machinery
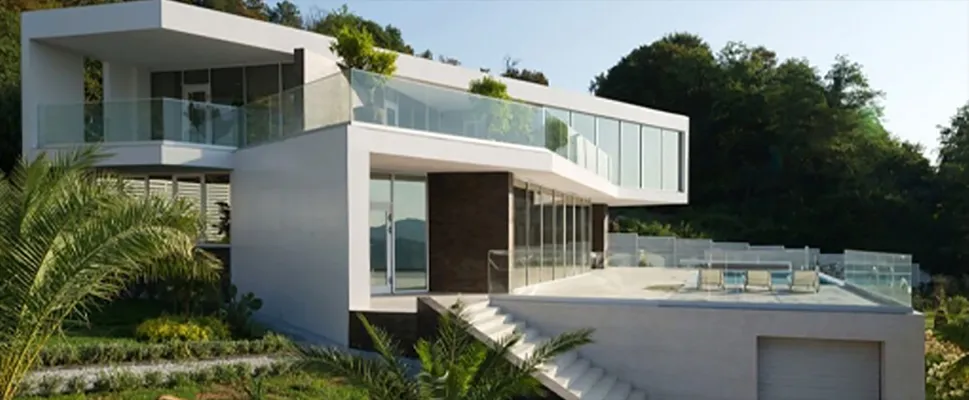
(textile weaving machine)
Revolutionizing Fabric Production Through Advanced Textile Weaving Machines
The global textile machinery market is projected to reach $46.2 billion by 2029 (CAGR 4.8%), driven by demand for automated weaving solutions. Modern textile weaving machine
s now achieve 94% operational efficiency, reducing fabric defects by 62% compared to 2018 models. This evolution directly addresses the 23% annual growth in technical textiles for automotive and medical sectors.
Breakthroughs in Textile Manufacturing Technology
Three core innovations dominate current development:
- Laser-guided shuttle systems improving weave accuracy to ±0.02mm
- Self-optimizing looms reducing energy consumption by 31%
- Integrated quality scanners detecting 0.1mm fabric irregularities
These advancements enable textile printing machines to achieve 1200 dpi resolution while maintaining 18-meter/minute production speeds.
Manufacturer Performance Analysis
Manufacturer | Weaving Speed (ppm) | Energy Use (kWh/m) | Maintenance Interval | Price Range |
---|---|---|---|---|
Picanol NV | 680 | 0.18 | 450h | $240k-$420k |
Dornier | 720 | 0.21 | 380h | $310k-$530k |
Tsudakoma | 650 | 0.16 | 500h | $210k-$390k |
Tailored Solutions for Specific Applications
Custom configurations address diverse requirements:
- Medical textiles: Sterilization-ready compacting machines with ISO Class 5 cleanroom compliance
- Automotive: High-tensile weaving heads for carbon fiber integration
- Fashion: Hybrid units combining digital printing and weaving in single workflow
Operational Efficiency Benchmarks
Latest compacting machines in textile production lines demonstrate:
- 38% reduction in thermal energy consumption (2023 vs. 2020 models)
- 22% faster fabric stabilization through adaptive pressure control
- Integration with IoT platforms reducing downtime by 57%
Implementation Success Stories
A Bangladesh denim mill achieved:
"83% faster style changeovers through automated textile printing machine presets, increasing monthly production capacity from 180,000m to 310,000m."
Smart Integration in Textile Weaving Machine Ecosystems
Forward-looking manufacturers now embed:
- Machine learning algorithms predicting maintenance needs with 89% accuracy
- Blockchain-integrated production tracking for supply chain transparency
- AR-assisted troubleshooting reducing technician deployment by 44%
This technological convergence positions modern textile weaving machines as central components in Industry 4.0 textile production frameworks.
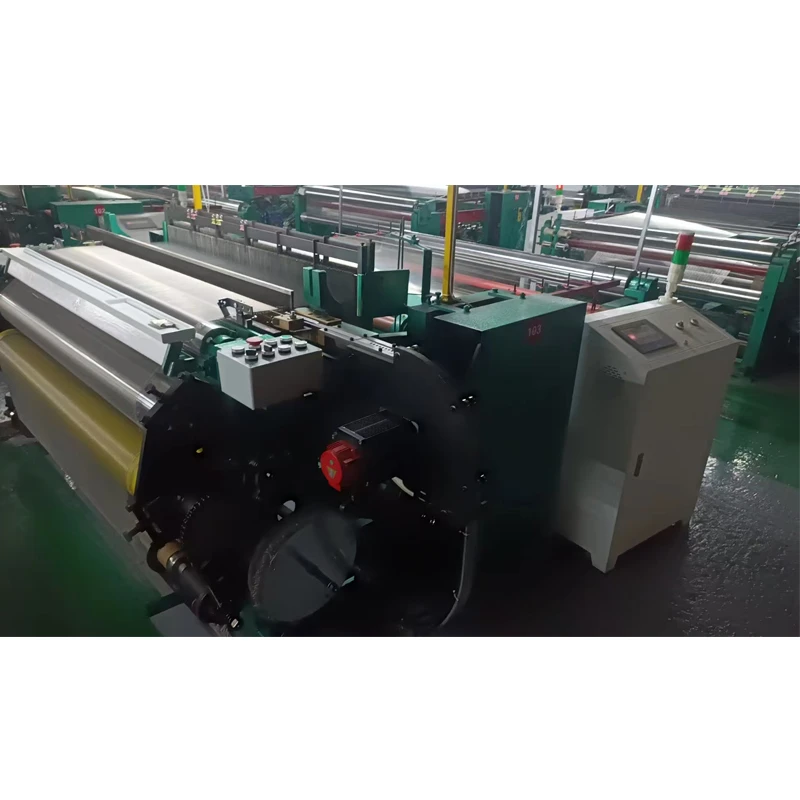
(textile weaving machine)
FAQS on textile weaving machine
Q: What is the primary function of a textile weaving machine?
A: A textile weaving machine interlaces warp and weft yarns to create fabrics. It automates the process for efficiency and precision. Modern versions often integrate digital controls for complex patterns.
Q: How does a textile printing machine differ from a weaving machine?
A: A textile printing machine applies designs or colors onto pre-woven fabrics. Unlike weaving machines, it doesn’t create the fabric structure. Techniques like screen, digital, or rotary printing are commonly used.
Q: What role does a compacting machine play in textile production?
A: A compacting machine shrinks and stabilizes fabrics to reduce residual shrinkage. It enhances fabric density and smoothness post-weaving. This step ensures consistent quality during garment manufacturing.
Q: Can textile weaving machines handle synthetic fibers?
A: Yes, modern textile weaving machines can process synthetic fibers like polyester or nylon. Adjustments to tension and speed may be required. Advanced models support hybrid yarns for diverse fabric types.
Q: Why is maintenance critical for textile printing machines?
A: Regular maintenance prevents ink clogs and ensures print accuracy. It extends the machine’s lifespan and reduces downtime. Neglect can lead to color inconsistencies or fabric waste.

Pervious