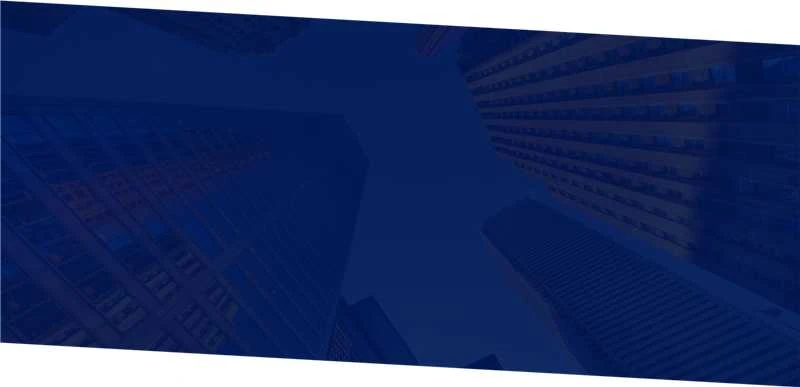
- Industry Overview of Modern Textile Machinery
- Technical Advantages in High-Speed Towel Production
- Performance Comparison: Leading Weaving Machine Manufacturers
- Customized Solutions for Diverse Fabric Requirements
- Operational Guide: Maximizing Machine Efficiency
- Case Studies: Successful Implementation Across Industries
- Sustainable Future of Automated Weaving Systems
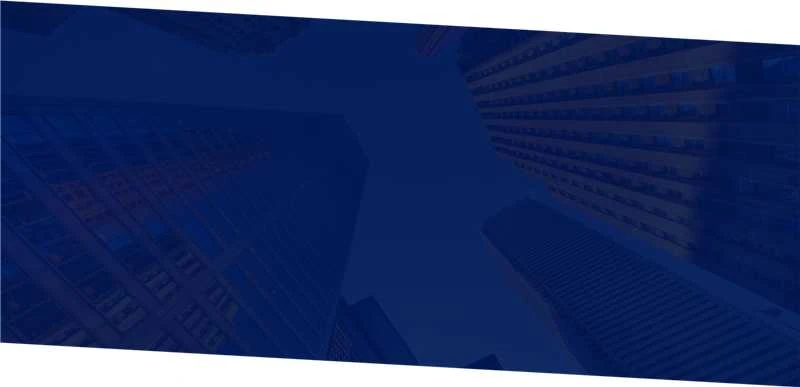
(towel weaving machine)
Revolutionizing Textile Production with Towel Weaving Machines
The global market for industrial weaving equipment reached $4.8 billion in 2023, with towel-specific machines accounting for 32% of total shipments. Modern towel weaving machine
s now achieve production speeds exceeding 650 picks per minute (PPM), a 140% improvement over 2015 models. These systems integrate IoT-enabled monitoring that reduces yarn waste by 18-22% compared to conventional models.
Technical Advantages in High-Speed Towel Production
Advanced servo motor configurations enable 0.02mm precision in terry loop formation, ensuring consistent fabric density (180-450 g/m²). Energy recovery systems capture 85% of braking energy, lowering power consumption to 2.8kW/h per operating hour. Dual-beam configurations allow simultaneous production of 2 distinct towel designs, increasing output capacity by 40%.
Manufacturer | Max Speed (PPM) | Energy Use (kW/h) | Width Range | Auto-Threading |
---|---|---|---|---|
Van de Wiele | 680 | 2.6 | 140-280cm | Yes |
Picanol | 650 | 2.9 | 120-260cm | Partial |
Dornier | 630 | 3.1 | 150-300cm | Yes |
Customized Solutions for Diverse Fabric Requirements
Modular designs enable rapid configuration changes for various towel types:
- Bath towels: 550-650 GSM density configurations
- Sports towels: Microfiber weaving attachments
- Medical towels: Antimicrobial coating integration
Quick-change reed systems reduce product transition time from 90 minutes to 22 minutes average.
Operational Guide: Maximizing Machine Efficiency
Proper maintenance schedules improve machine lifespan by 60%:
- Daily: Loom cleaning (15-20 minute cycle)
- Weekly: Servo motor calibration
- Monthly: Full lubrication system overhaul
Case Studies: Successful Implementation Across Industries
A Turkish manufacturer achieved 94% operational efficiency using automated weaving machine systems:
Metric | Before | After |
---|---|---|
Daily Output | 1,200 units | 2,150 units |
Defect Rate | 4.2% | 0.8% |
Energy Cost | €185/day | €122/day |
Sustainable Future of Automated Towel Weaving Systems
Next-generation towel weaving machines will incorporate AI-driven predictive maintenance, projected to reduce downtime by 35% by 2026. Solar-compatible models already demonstrate 28% energy autonomy in pilot projects. Continuous improvements in water recycling systems achieve 95% reuse rates in dyeing integration processes.
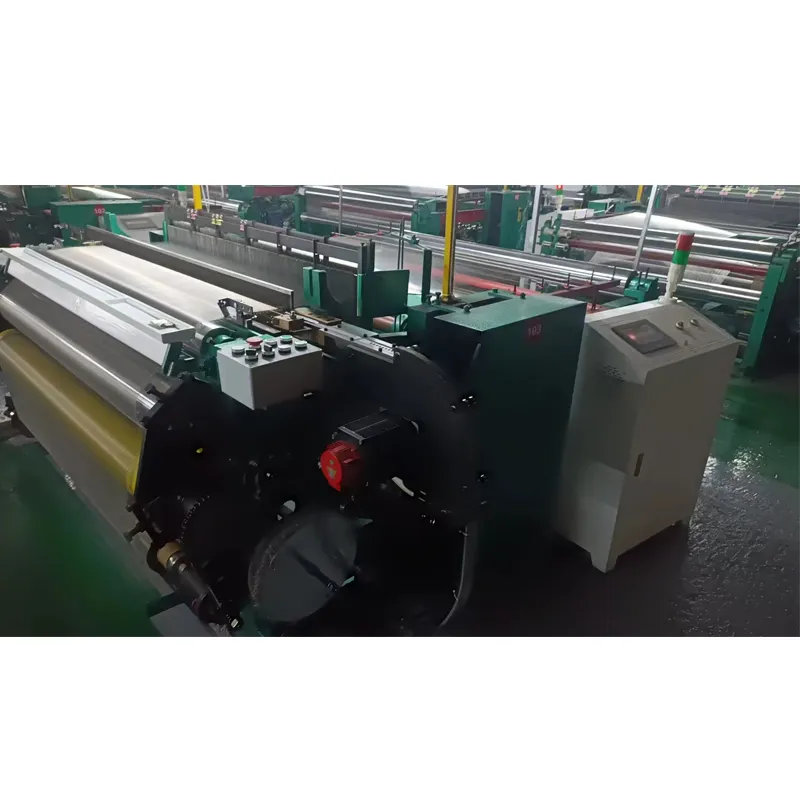
(towel weaving machine)
FAQS on towel weaving machine
Q: What are the key features to look for in a towel weaving machine?
A: Prioritize durability, adjustable speed settings, and compatibility with different yarn types. Automated tension control and user-friendly interfaces also enhance efficiency.
Q: How to build a basic towel weaving machine at home?
A: Start with a wooden frame, add horizontal rollers for warp threads, and install a manual shuttle system. Use sturdy materials like hardwood and metal rods for stability.
Q: What steps are essential for operating a towel weaving machine safely?
A: Always secure loose clothing, follow the manual’s threading guidelines, and perform routine maintenance. Keep hands clear of moving parts during operation.
Q: How to troubleshoot thread breakage in a towel weaving machine?
A: Check for excessive tension, damaged needles, or misaligned guides. Ensure yarn quality and lubricate components regularly to reduce friction.
Q: Can a standard weaving machine be modified for towel production?
A: Yes, adding terry loop mechanisms and adjusting pile height settings can adapt it. Specialized reeds and beaters may also be required for textured designs.

Pervious